Reverse engineering: evaluating the design and function of existing products
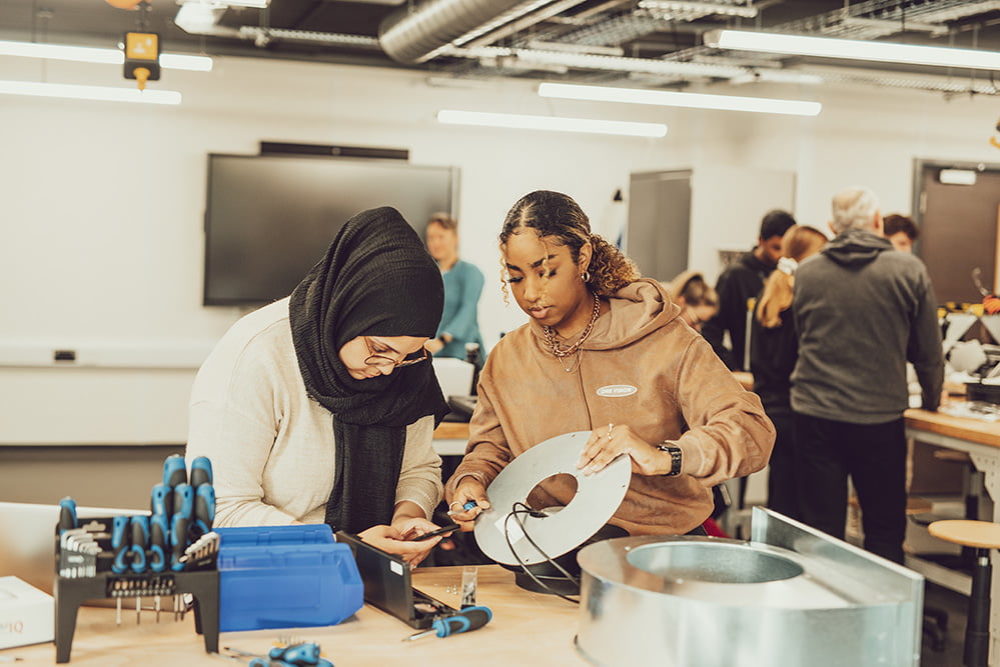
It is easy to assume that everyday products are the best design possible, but how do we know whether this is definitely the case? Understanding how existing products and solutions are designed and improving them for the future is a key element of engineering.
Reverse engineering for design
For their second project, TEDI-London students used reverse engineering techniques to take apart a Heat Recovery Ventilator (HRV) unit, a key component of the TEDI-London campus energy efficiency system. A HRV is a device that replaces the stale air inside a building with fresh air from outside, whilst simultaneously recovering the heat that would usually be lost during the ventilation process.
In this project, students developed their understanding of some of the most fundamental aspects of engineering, such as analytical, measurement and experimental investigation techniques, in a hands-on and practical way. Taking the unit apart helped them to learn about each individual internal component, how they fit together, and the overall requirements of the unit. Our students were tasked not only with identifying part functions, but also with creating a technical document to record the parts’ locations in the assembly, analysing the product’s ability to meet customer needs and suggesting improvements. Each of these skills is useful at key stages of the design processes that engineers have to go through in the workplace.
Which tools were needed to disassemble the units?
In teams, students had a HRV unit to reverse engineer, each of which was a different type and make. They had access to detailed information about the materials and components that made up their HRV, including weight, dimensions, material properties like density and heat capacity and cost, as well as a checklist of criteria to be met, such as price, sustainability, durability and health and safety. The students used pen and paper to sketch initial drawings of the HRV’s and their internal parts, as well as CAD software to visually represent how each unit’s components were taken apart and fitted back together.
Finally, they were provided with a kit of basic tools to dismantle their units:
Spanners: these were useful for undoing the nuts and bolts that held the outside casing of the HRV’s together, allowing the students to access the internal parts.
Screwdrivers and hex keys: these were used to detach some of the internal parts so that students could look more closely at them.
Tape measures and rulers: tape measures helped with working out the overall HRV dimensions, whilst the rulers were useful for creating product and component sketches by hand.
Digital and vernier callipers: both designed to take measurements extremely accurately, the students found callipers useful when it came to working out the dimensions of the more intricate internal components, such as fan blade widths or screw hole diameters.
Taking apart a real engineered product allowed students to identify the benefits and drawbacks of different designs and put vital industry skills into practice. By putting forward their own ideas on how the HRV’s could be made better, they also improved their ability to think creatively, prioritise and present their findings to their peers.
Student reflections
Explaining what she thought of the project, TEDI-London student Rozanne shares: “The reverse engineering project is amazing. I hadn’t realised how complex some of the products that we use day-to-day are, and it wasn’t until I actually took the unit apart that I started to think in more detail about how things work. It was very enlightening and made me ask so many questions that I wouldn’t have thought to ask if I was in a lecture environment or just reading theory.”
Keen to learn what other TEDI-London projects are like? Read about students’ first-term project, the Engineering for People Design Challenge.
More News articles
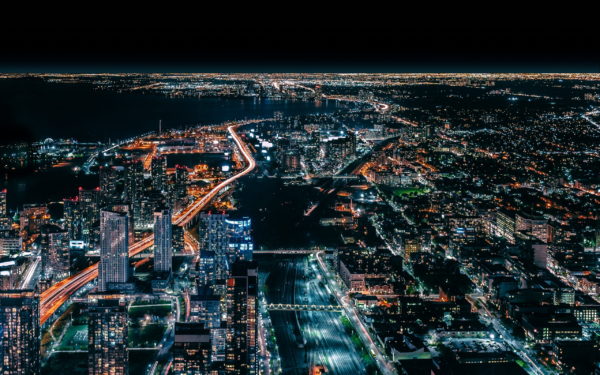
What types of projects could you study at TEDI-London?
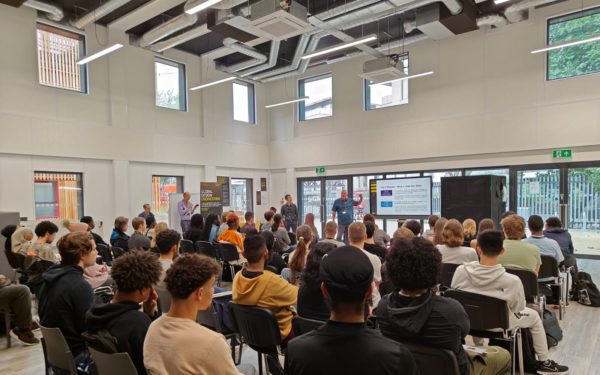